Diamond BH Series
This dual-drive hybrid makes short work of any project with long-term, high-speed, energy-efficient operation.
When you need lightning-fast, highly precise processing, hybrid press brakes are up to the task. But what sets our BH series hybrid press brakes apart from the pack?
When it comes to repeat/stop accuracy, easy operation, or keeping your shop operating more cost-efficiently than you might have previously thought possible—without sacrificing quality, capability, or speed—the BH series bends the rules just as easily as it bends thick material with the ease of thin gauged material all while maintaining the tightest of tolerances.
World-class productivity achieved through our proprietary technology results in greater reliability, machine uptime, and reduced operational costs and ease of operation – part after part, year after year – experience the difference with the BH series.
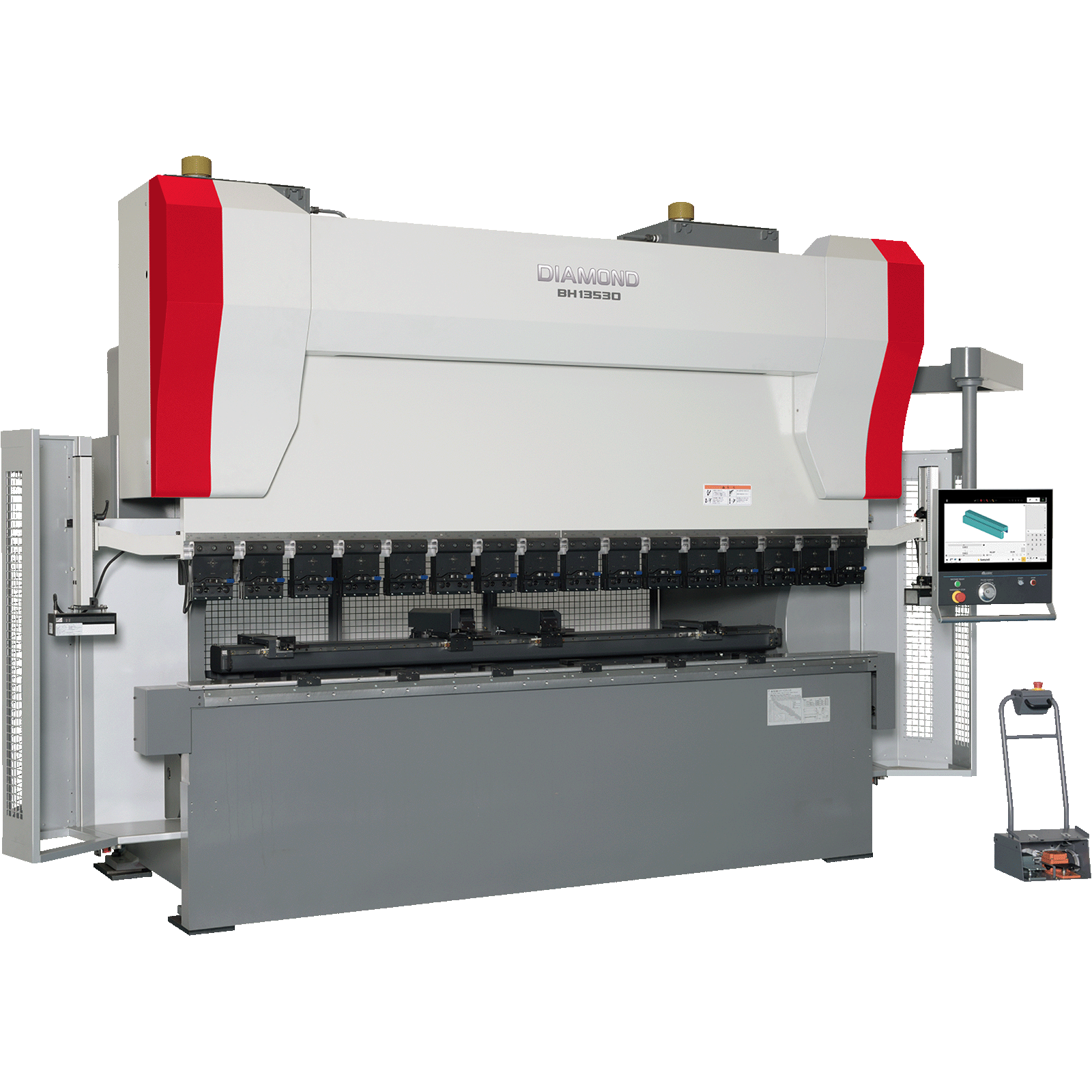
- The electric AC servo motor hybrid and ball screw drive mechanism isn’t just fun to say. It achieves performance that outclasses other electric and hybrid press brakes, all while ensuring long-term accuracy and minimum internal wear. The result? A machine you can trust to keep doing everything you need it to, day after day.
COST-EFFICIENT OPERATION
- Form complex parts easily and cost-efficiently. The BH series is built from the ground up to deliver the best results with the fewest required resources. It’s soft on electricity consumption but still tough on any project your shop can throw at it.
MAXIMUM RESULTS, MINIMUM EFFORT
- An easy, intuitive 22” color multi-touchscreen running Windows makes everything from day-to-day operation and programming to 3D simulation simple and quick. That means that this machine has the potential to achieve peak performance in nearly any scenario under any operator. Finally—simple, stress-free functionality.
- The Diamond BH dual-drive system controls high-speed up/down movement with a ball screw and bending movement by the servo-hybrid piston system for unbeatable functionality.
- The dual drive system allows high-speed down movement at 200 mm per second with high repeat-stop accuracy while still offering energy savings thanks to an assist device that stores the energy of down movement for the industry’s fastest cycle time 2.3s.
- The ram floats on a gas cushion, thereby greatly diminishing the weight to return the ram to the top of the stroke, resulting in lower operational costs for greater cost-efficiency.
- Ram cylinders powered by AC servo motors with 1 micron repeat accuracy and combined with a back gauge, accurate down to 4 microns, the BH Series delivers positioning accuracy unparalleled in the industry, part after part.
- With automatic thickness detection & compensation, angular irregularities are minimized due to material thickness with no added options or external measurement device needed; the BH series holds tolerances some machines can only hope to do with angle measurement systems.
COMPONENTS:
- Dual-drive hybrid (ram positioning by electric ball screw and hybrid piston system) with highly stable repeat accuracy (1-micron repeat accuracy) +001mm
- High-speed dual-drive hybrid (fastest cycle time in its class)
- Large stroke and open height
- Patented automatic micro-wedge crowning system (standard)
- Standard 5-axis back gauge on 2.5/3m (optional 7- & 9-axis back gauges available)
- Standard 7-axis back gauge on 4m (optional 9-axis back gauge available)
- LED lighting over the back gauge and front work area (standard)
- Pulse handle with axis control & bending support (standard)
- 5” X-axis max gauge distance (4-micron back gauge repeat accuracy) +0.004mm
- Simple up/down foot pedal safety system (standard)
- Interlocked rear access gate (standard)
- Mitsubishi servo amplifiers and motors
- One-touch European tool holders (standard) – WATCH VIDEO
ON-BOARD PRODUCTIVITY:
- Automatic thickness detection/compensation capabilities for accurately measuring part thickness on the fly
- Work efficiency analysis capabilities to ensure you’re always working at peak production
USER INTERFACE:
- USB & Lan peripheral interfacing
- CNC control with 22” multi-touchscreen LCD display with 3D simulation, 2D/3D draw functionality, and custom multiuser & multilanguage interface
SYSTEM INFORMATION:
- Microsoft Windows operating system (16GB)
- Large program capacity (64GB) with a comprehensive tool library
OPTIONAL COMPONENTS:
- Angle measurement
- Sheet followers (75 kg and 150 kg)
- Sheet supports
- Moveable foot pedal
- Tandem foot pedal
- Laser finger guarding
- Extra CNC back gauge axes (up to 9 axes)
- Hydraulic clamping from Wila and Wilson
- Back gauge touch sensors
- Tooling packages from Wila, Wilson and Mate
- Interlocked side gates over the C-frames
- American segmented upper punch holders
- Small segmented European punch holders
- DiamondBend offline programming software – WATCH VIDEO
- Automatic tool changer
- VIDERE operator support system
- Increased throat
- Increased open height
- Bar code reader
MODEL | BH8525 | BH13530 | BH18530 | BH18540 | BH25030 | BH25040 |
Press Force: metric (US) | 85 (94) | 135 (149) | 185 (204) | 185 (204) | 250 (276) | 250 (276) |
Bending Length: mm (in) | 2,600 (102) | 3,100 (122) | 3,100 (122) | 4,100 (161) | 3,100 (122) | 4,100 (161) |
Back Gauge Axis | 5/7/9 | 5/7/9 | 5/7/9 | 7/9 | 5/7/9 | 7/9 |
Open Height: mm (in) | 530 (21) | |||||
Ram Stroke: mm (in) | 250 (10) | |||||
Gap Depth: mm (in) | 400 (16) | |||||
Distance Between Frames: mm (in) | 2,200 (87) | 2,700 (106) | 2,700 (106) | 3,700 (146) | 2,700 (106) | 3,700 (146) |
Strokes/Hour (SPH) | 1,565 |
RELATED SOLUTIONS
-
ELECTRIC PRESS BRAKES
Mitsubishi electric press brakes are known for speed, efficiency, and reliability.
learn more -
HYBRID PRESS BRAKES
This Mitsubishi dual-drive hybrid press brake makes short work of any project with its high speed, energy-efficient operation.
learn more -
HYDRAULIC PRESS BRAKES
High productivity, heavy-duty bending performance, and intuitive operation in a cost-efficient package.
learn more -
PRESS BRAKE AUTOMATION
Real-time information from this game-changing Mitsubishi tool changer lets any press brake operator perform at their best.
learn more
-
"The accuracy and repeatability are outstanding. I had one job running for five days straight—there was no difference from the first part bent on day one to the last part bent on day five. All of this plus the reduced setup time translates into higher profitability."
Milan Popik Jr, Owner at Metal Tronics view case study -
"“Press brake operators of all skill levels can easily set up complex jobs. This saves tremendous time and resources. Press brakes have not changed that much mechanically over the years, but technology like automation and diagnostics can really set you apart from the competition."
Eugenio Martin, Lynam Inc. manufacturing engineering manager