By MC Machinery Senior Laser Applications Manager Michael Koch
Doing more with less is the name of the game in laser cutting—and will be for the foreseeable future.
With an ongoing labor shortage, fluctuating metal prices, increasing demand and smaller profit margins, technology is advancing rapidly to help fabricators succeed amidst these challenges.
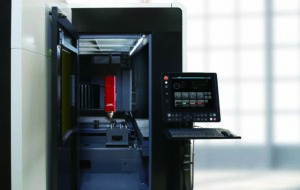
The Mitsubishi GX-F ADVANCED AI-enabled fiber laser can track more than 300 cut conditions for nearly any kind of material and gauge.
While some manufacturers focus on speed, that’s not as important as machines that can do more with less and are easy to operate no matter the skill level.
The most important technology for the future of laser cutting includes:
● Software that allows hands-off management of the production process and maximizes material use while reducing scrap. Nesting algorithms in programming software continue to grow and become more dynamic, ranging from static nests that match the flow of work to nesting that accommodates multiple jobs on the same sheet of material. Mitsubishi’s DiamondFAB solution provides full ERP integration, nesting, scheduling, workflow management, automation control and part sorting.
● Lasers with intuitive controls, artificial intelligence and augmented reality. Mitsubishi’s GX-F ADVANCED fiber laser features a cutting head with a camera and microphone, serving as the eyes and ears that watch and listen to the cutting process. The GX-F ADVANCED AI-enabled fiber laser can track more than 300 cut conditions for nearly any kind of material and gauge.
● Automation systems that not only load and unload fast enough to keep up with lasers, but also have rotary heads with multiple tools to accommodate different sizes/weights. These systems can pick up a sheet from a pallet, separate stuck sheets if necessary, measure the thickness and deliver it to the worktable in under a minute. Since most lasers won’t be finished cutting a sheet in under a minute, automation prevents the laser from ever being idle.
● Part-sorting software that can determine the order of parts being picked up, assign orientation for downstream operations, and more. The Astes4 High Speed Skyway is capable of controlling the entire production process, from loading material to storing parts. Sheets are loaded with suction cups and then parts are cut. Cartesian grippers then move in to independently pick out assigned parts and sort them on the correct pallet, which is transported to the corresponding next process.