Electrical discharge machining (EDM) is a process used to cut and shape hard materials that cannot be performed by traditional machining. EDM works by eroding materials with an electric spark to create a precise cut without touching the work material.
There are a few different variations, but the two main types are wire EDM and sinker EDM.
What is EDM?
EDM was invented in the 1950s and has become more widely used as technology has advanced. What makes EDM different than traditional machining is that cuts are made without physically touching the material.
EDM is used on electrically conductive metals and can cut through hard metals such as titanium, hardened steel and tungsten without the chatter and vibrations of traditional machining. EDM can also make highly precise cuts.
What is Sinker EDM?
Sinker EDM, which is also called ram EDM, volume EDM and cavity EDM, is a type of EDM used to produce cavities in metal workpieces. This is done using an electrode tool that is the shape of the cavity being created. The shaping tool, or die, can be machined to create complex positive shapes that are then used to erode materials from the workpiece to create the cavity. These tools are generally made out of materials like graphite, tungsten and copper.
For sinker EDM, the electrode and workpiece are immersed in insulating fluid and linked with a power supply. The workpiece and electrode must be alternatively positively or negatively charged. As the electrode approaches the workpiece, an electric spark forms between them at a temperature between 14,400°F (8,000°C) and 21,600°F (12,000°C), vaporizing the metal in the localized region. The electrode does not cut entirely through the metal, but instead cuts out the cavity with no material stress. Sinker EDM can create intricately shaped cavities that can be used as injection molds and stamping dies.
Advantages of Sinker EDM
There are several advantages to using sinker EDM for certain applications:
-
- The sinker EDM process does not require a tool made out of materials that are harder than the workpiece like other types of machining.
- This process can create features with irregularly shaped holes.
- Using a precisely machined electrode, sinker EDM can create accurate cavities.
- The electrode tool does not experience loads that could bend or deform it, which allows for more controlled accuracy.
- Any metal that is conductive can be machined with the sinker EDM process.
Applications of Sinker EDM
Sinker EDM can create accurate, complex cavities better than other machining processes and is especially useful on hard materials. It is most suitable for the following applications:
-
- Dies
- Mold making
- Medical
- Aerospace
- Rapid tooling
- Energy
- Power generation
- Deep and thin ribs
- Sub gate
- Thread
- Internal splines
- Blind cavities
- Blind keyways
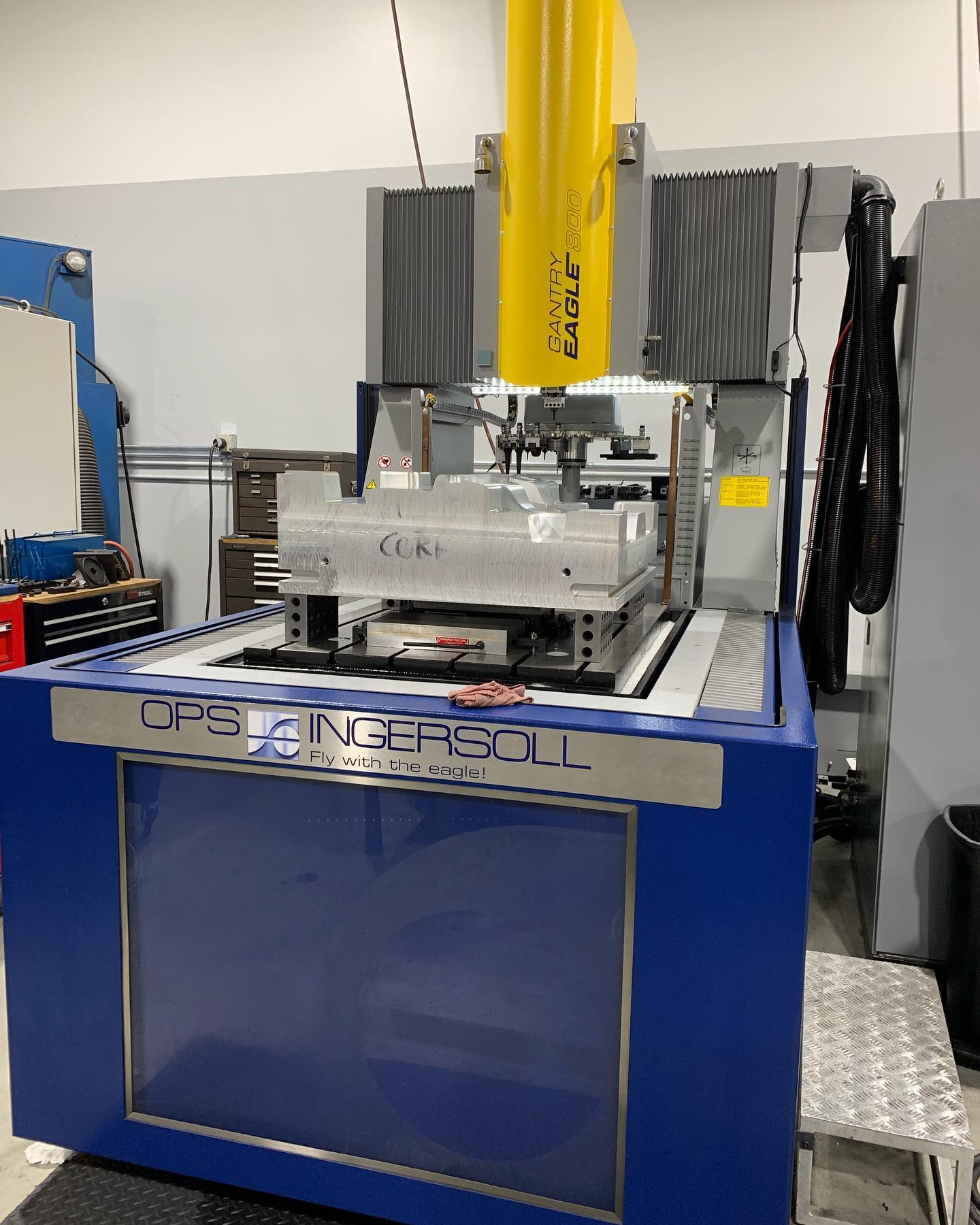
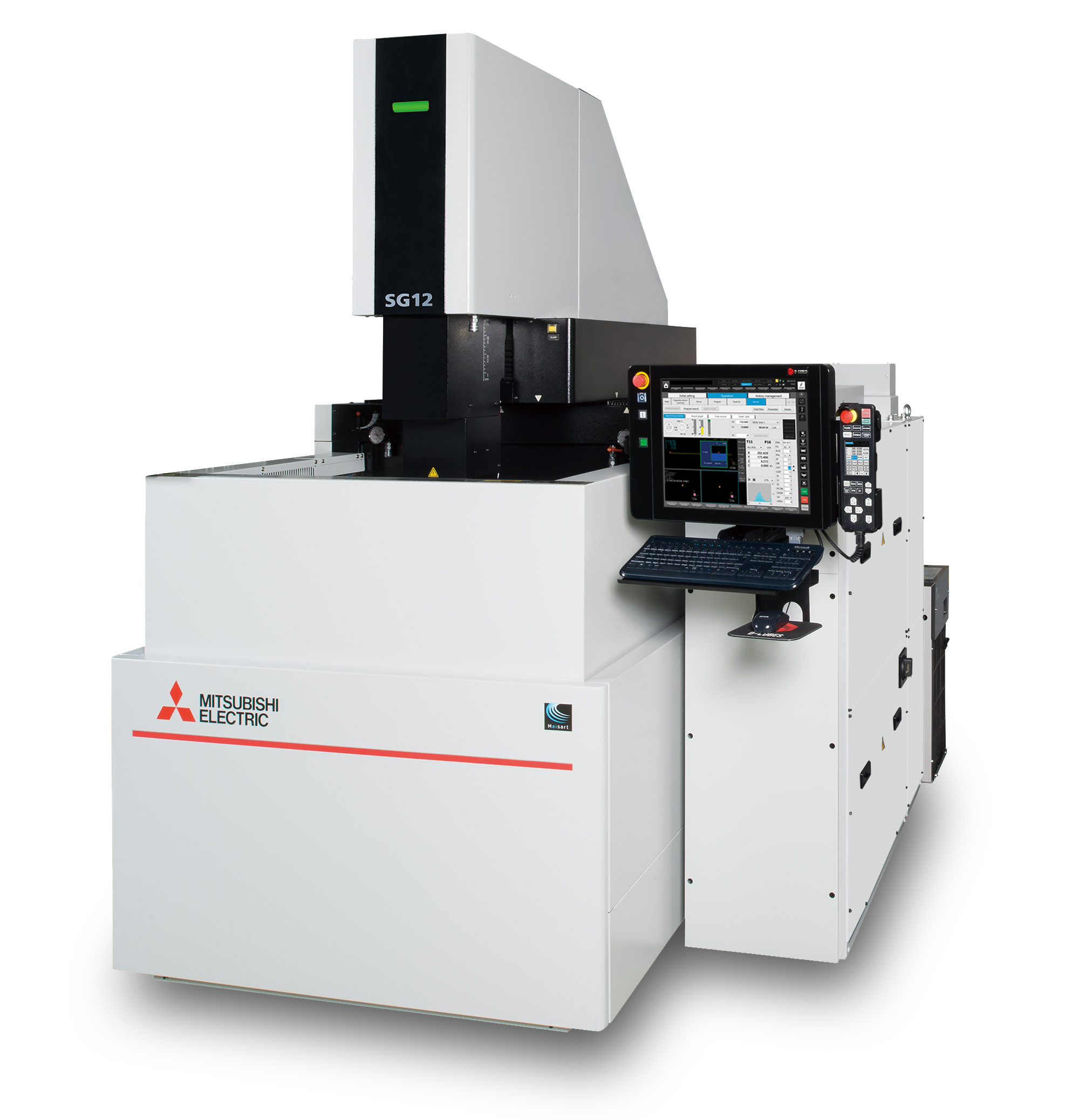
What is Wire EDM?
Wire EDM, also known as wire-cut EDM and wire cutting, is a process in which a thin, single-strand wire cuts through the workpiece using thousands of sparks without making physical contact with the workpiece.
The wires are typically made of brass, while deionized water is most often used as dielectric fluid. The wire is held between two diamond guides, with one positioned below the workpiece and the other positioned above. The guides get instructions from the CNC and move the wire along the X and Y axes to make the desired cut. The sparks between the wire and workpiece are caused by current discharges that erode the material. The wire also erodes during the process and is constantly refreshed as it moves along a supply spool.
The exact cuts provided by wire EDM allow for the execution of complex cuts and designs. Wire EDM can be used to cut steel, carbide, aluminum, titanium, Inconel, PCD, graphite and other conductive materials.
Advantages of Wire EDM
There are many advantages to using the wire EDM process:
-
- Wire EDM creates two-dimensional cuts on three-dimensional parts.
- This process can make extremely accurate cuts and create fine, complicated structures.
- Wire EDM can be used to manufacture molds and dies.
- This process is best suited for sample preparation and high-precision cutting.
- Wire EDM is the most cost effective for small production.
- The precise and accurate cuts of wire EDM eliminate the need for additional processing and finishing of the workpiece.
- This process can create complex designs and shapes that CNC machining cannot create easily.
- Wire EDM is less stressful on workpieces than traditional machining which makes it ideal for fragile materials.
- This process can cut small parts and highly detailed items that other types of machining cannot perform.
- The wire EDM process is continuous—there are no interruptions, even if a wire breaks.
- Tool electrode: The wire EDM process uses a wire made from brass as the tool electrode, while the sinker EDM process uses an electrode made from graphite, copper and copper tungsten.
- Dimensional cutting: The wire EDM process is best suited for two-dimensional cutting while the sinker EDM process can be used to create complex three-dimensional shapes for cavities.
- Efficiency: The wire EDM process is quick and efficient as the machine is ready once the wire is in place. For the sinker EDM process, a tool electrode must be made first in the shape of the desired cavity.
- Blind features: Wire EDM cannot produce blind features and is best for profile cutting with through holes. Sinker EDM can produce blind features including holes and cavities that don’t open on the bottom end.
- Start point: Wire EDM must be started from the edges unless you create a through hole on the workpiece to start the wire. Sinker EDM can be started from anywhere on the workpiece.
- Cut types: Wire EDM is ideal for high-precision profile cutting, angular cutting and separating or splitting off. Sinker EDM is ideal for finishing, drilling, deburring and 3D contouring.
- Wire EDM cuts materials without causing burrs or distortion in just one processing stage.